Radars, robots and roller coasters through the wringer
Performing climatological, electromagnetic and mechanical assessments, Thales’ Environmental Competence Center puts a wide range of products to the test, from antennas to art objects. Harry Vorderman runs this business within a business.
Few visitors to a museum will realize it, but without the proper precautions, they may inadvertently damage the pieces of art they’ve come to admire. The vibrations they generate just by walking past a display case can already have detrimental effects on the objects contained inside. At Thales’ Environmental Competence Center (ECC), these effects can be mapped out, so that appropriate countermeasures can be taken, like installing special suspension systems.
“In our vibration chamber, we test how much artifacts can take before they break. By subjecting them to different patterns of shaking and even shocks, we can simulate all kinds of stressful events, not only crowd movements but also transportation,” says ECC director Harry Vorderman. “As these tests are potentially destructive, we obviously don’t unleash them on the real thing. Instead, we’re given representative dummies to experiment with – exact replicas, already damaged specimens or otherwise dispensable pieces in a collection.”
The ECC’s main activities also include EMC and climatological testing. “Next to performing vibration, shock and other mechanical analyses, we measure how electronic equipment functions in its electromagnetic environment and how it behaves under extreme weather conditions,” Vorderman clarifies. “We do that for Thales but also for a wide range of external clients – we’re more or less a little company within a big company.”
Unexpected behaviour
In Hengelo, Vorderman and his team have an advanced EMC laboratory at their disposal. “Our standard test for military-grade equipment covers the frequency range from 30 Hz to 18 GHz. On special request, we can even go as high as 40 GHz. Non-military applications normally stay well below that. There, a couple of gigahertz suffices – we recently bought a new antenna that allows us to scan radiated emission in one run from 30 MHz to 6 GHz for such systems.”
In addition to the standard EMC tests, the ECC is also equipped to perform Tempest measurements. Tempest is a US National Security Agency specification and a NATO certification regulating the level of unintentionally generated signals that may give away sensitive information. “It’s a much stricter EMC test to check if products are sufficiently shielded to prevent this unwanted leakage,” Vorderman explains.
Although the EMC chamber can easily fit a Thales radar, it isn’t large enough for all tests. On occasion, Vorderman’s team therefore performs EMC measurements at customer sites as well. “Some time ago, the Dutch army contacted us about a vehicle that was exhibiting unexpected behavior, responding to radio frequencies it shouldn’t be responding to. Together, we found out which frequencies were responsible for this behaviour and the army can now notify the manufacturer to solve the problem.”
“The Dutch army also has selected the multi-mission radar from Thales Netherlands for mounting on a truck. They’ve requested us to measure the radiation levels in the cabin of the vehicle. They want to know whether it’s safe for their personnel to remain inside while the MMR is in operation. As the whole thing is too big for our lab, we’re going to drive it into a test field and measure the radiation levels there.”
Burning heat
In the ECC’s climate chamber, equipment is exposed to all kinds of harsh environments. “We can simulate a wide range of climates, including cold, hot, extremely sunny, humid or dusty,” illustrates Vorderman. “For aerospace customers, we also run vacuum tests and for maritime applications, we offer the option of immersing them in the salt spray often encountered by ships at sea.”
Recently, the ECC was approached by a manufacturer of amusement rides to test parts of a roller coaster for a theme park in Dubai. “They brought in a collection of metal and plastic elements, which we then exposed to a desert climate,” Vorderman recalls. “The test revealed that the materials that had been chosen because they work fine in a typical European environment aren’t suitable at all over there. Because of the intense solar radiation, they get so hot that they burn the skin on contact. Also, the designer had picked a black-and-white color scheme, but we showed that that’s not the best choice in the Middle Eastern heat.”
On behalf of maritime clients, the ECC often performs so-called type approvals. These require a broad range of tests, including climate, EMC and mechanical measurements. The results are submitted for validation by a certifying body like DNV or Lloyd’s and only after they’ve issued a certificate may a product be sold for use on a ship.
One of Vorderman’s maritime customers is Kwant Controls, a leading manufacturer of nautical propulsion control systems. “A ship used to have only one large mechanical helm. Nowadays, with bridges tens of meters wide, a captain has multiple interconnected joysticks, one every five meters, to steer the vessel. Kwant brings this equipment to us to have it assessed for DNV compliance.”
A bit of everything
The ECC is quite a departure from Vorderman’s previous job as industrial partnership and purchasing manager at Thales. “For more than twenty years, I traveled the world to negotiate and maintain long-term export relationships. During the many hotel stays, I was quick to pick up my computer and do some more work, so I made long days. When I joined the ECC in 2019, I had to adjust to the 9-to-5 rhythm, but since I’ve got used to it, I’m enjoying the relative peace of mind it has brought me.”
As the manager of the ECC, Vorderman can more or less determine his own course. “We run a specialised business, relatively independently from the rest of Thales. It’s great to have that freedom while at the same time being able to rely on company services like HR and legal. I like that I can do a bit of everything: finance, purchasing, sales and now also technology. I’m not an engineer by education – I had to read up on things like EMC, mechanical tests and product standards – but I really enjoy my front-seat view of the latest technological developments, both from Thales and other companies.”
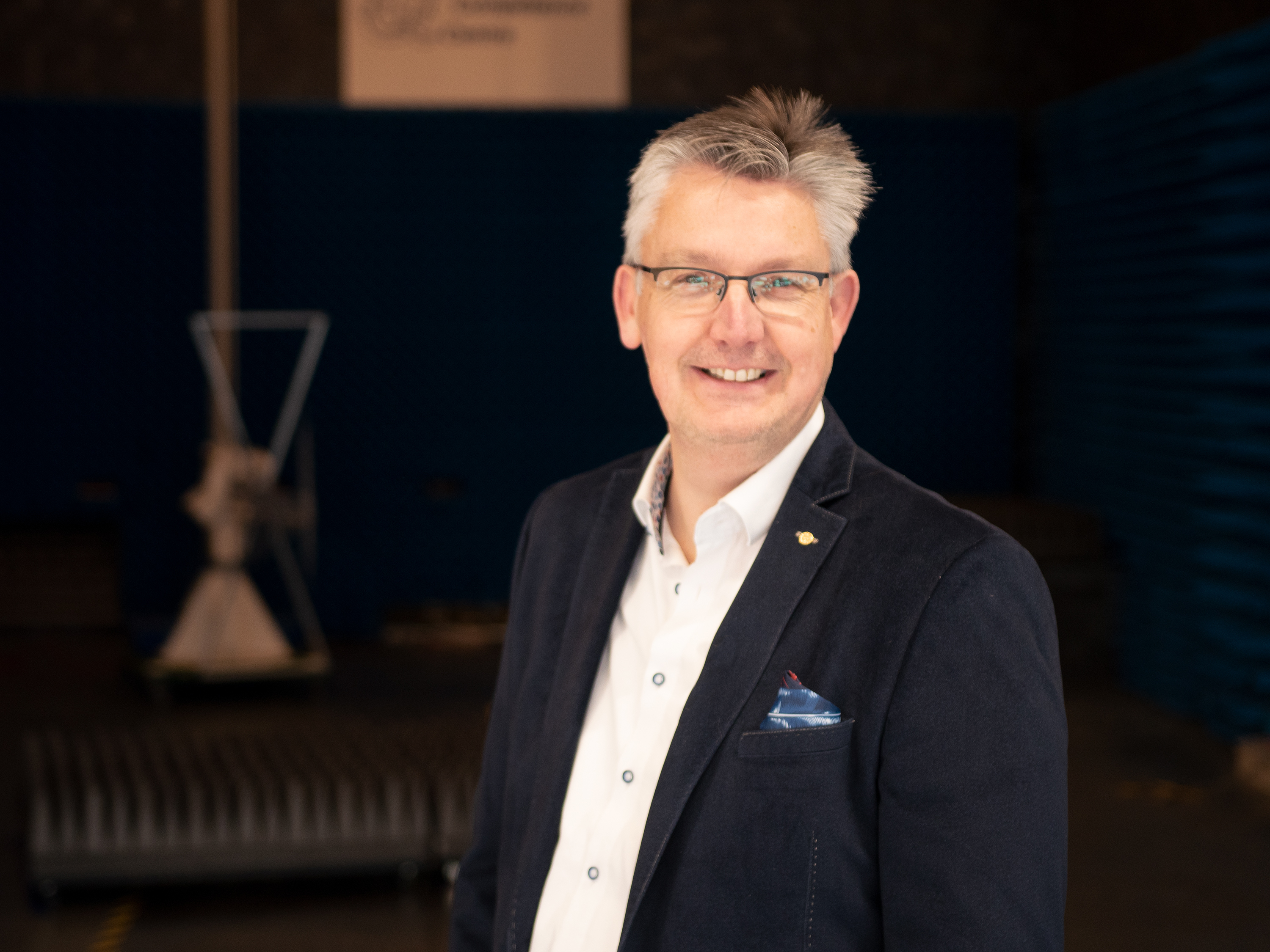